The inherent risks of oil and gas drilling operations are daunting, with the most severe being the uncertainty of downhole pressure. According to the International Association of Drilling Contractors, Managed Pressure Drilling (MPD) is an adaptive drilling technique used to precisely control the annular pressure throughout the entire wellbore. Over the past fifty years, many technologies and methods have been developed and refined to mitigate and overcome the challenges brought by pressure uncertainty. Since the introduction of the first Rotating Control Device (RCD) globally in 1968, Weatherford has been a pioneer in the industry.
As a leader in the MPD industry, Weatherford has innovatively developed various solutions and technologies to expand the range and application of pressure control. However, pressure control is not just about controlling annular pressure. It must take into account countless special operational conditions worldwide, complex formations, and challenges at different wellsite locations. With decades of accumulated experience, the company's technical experts realize that an excellent pressure control process should be tailored to address different challenges rather than being a one-size-fits-all system for any application. Guided by this principle, MPD technologies of different levels have been developed to meet the various needs of operating companies, regardless of how challenging their conditions or environments may be.
01. Creating a Closed-Loop System Using RCD
RCD provides both safety assurance and flow diversion, serving as an entry-level technology for MPD. Originally developed in the 1960s for onshore operations, RCDs are designed to divert flow on top of BOP to create a closed-loop circulation system. The company has continually innovated and improved RCD technology, achieving field-proven success over several decades.
As MPD applications expand into more challenging fields (such as new environments and challenges), higher demands are placed on MPD systems. This has driven continuous advancement in RCD technology, which now features higher rated pressures and temperatures, even obtaining qualifications for use in pure gas conditions from the American Petroleum Institute. For example, Weatherford's polyurethane high-temperature sealing components have a 60% higher rated temperature compared to existing polyurethane components.
With the maturity of the energy industry and the development of offshore markets, Weatherford has developed new types of RCDs to address the unique challenges of shallow and deepwater environments. RCDs used on shallow-water drilling platforms are positioned above the surface BOP, while on dynamically positioned drilling vessels, RCDs are typically installed below the tension ring as part of the riser assembly. Regardless of the application or environment, RCD remains a critical technology, maintaining constant annular pressure during drilling operations, forming pressure-resistant barriers, preventing drilling hazards, and controlling the invasion of formation fluids.
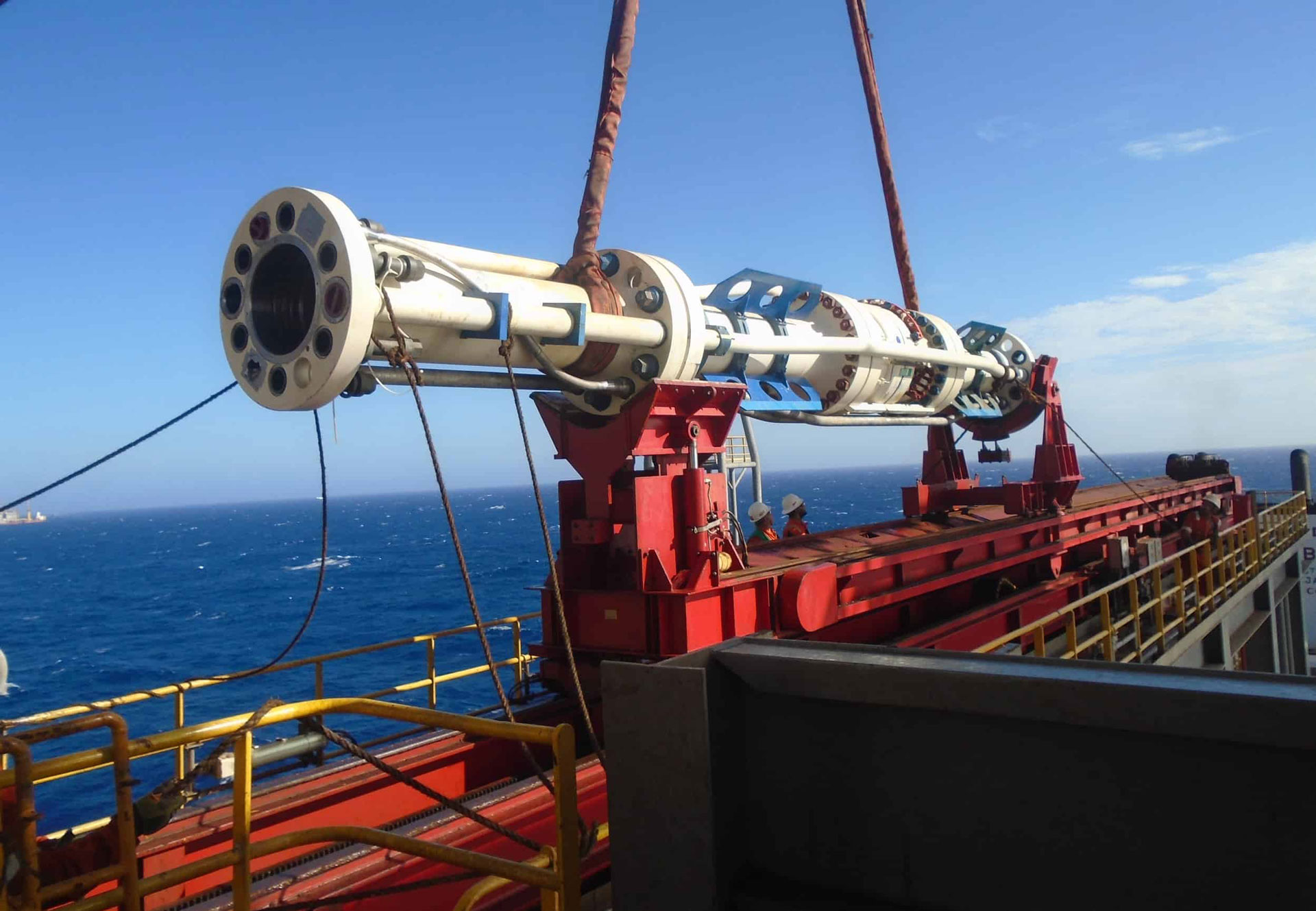
02. Adding Choke Valves for Better Pressure Control
While RCDs can divert returning fluids, the ability to actively control the pressure profile of the wellbore is achieved by downstream surface equipment, particularly choke valves. Combining this equipment with RCDs enables MPD technology, providing stronger control over wellhead pressures. Weatherford's PressurePro Managed Pressure solution, when used in conjunction with RCDs, enhances drilling capabilities while avoiding pressure-related incidents downhole.
This system utilizes a single Human-Machine Interface (HMI) to control the choke valves. The HMI is displayed on a laptop in the driller's cabin or on the rig floor, allowing field personnel to virtually control the choke valves while monitoring crucial drilling parameters. Operators input the desired pressure value, and then the PressurePro system automatically maintains that pressure by controlling the SBP. The choke valves can be automatically adjusted based on changes in downhole pressure, enabling fast and reliable system corrections.
03. Automatic Response for Reduced Drilling Risks

The Victus Intelligent MPD Solution stands as one of Weatherford's most significant MPD products and one of the most advanced MPD technologies in the market. Built upon Weatherford's mature RCD and choke valve technologies, this solution elevates precision, control, and automation to unprecedented levels. By integrating drilling rig equipment, it enables communication between machines, real-time analysis of well conditions, and rapid automatic responses from a centralized location, thereby accurately maintaining bottomhole pressure.
On the equipment front, the Victus solution enhances flow and density measurement capabilities by incorporating Coriolis mass flow meters and a manifold with four independently controlled choke valves. Advanced hydraulic models consider fluid and formation temperatures, fluid compressibility, and wellbore cuttings effects to precisely determine real-time bottomhole pressure. Artificial intelligence (AI) control algorithms identify wellbore anomalies, alerting the driller and MPD operators, and automatically sending adjustment commands to MPD surface equipment. This allows for real-time detection of wellbore influx/losses and enables appropriate adjustments to equipment based on hydraulic modeling and intelligent control, all without the need for manual input from operators. The system, based on programmable logic controllers (PLCs), can easily integrate at any location on the drilling platform to provide reliable, secure MPD infrastructure.
A simplified user interface helps users stay focused on key parameters and issue alerts for sudden events. Status-based monitoring tracks the performance of MPD equipment, enabling proactive maintenance. Reliable automated reporting, such as daily summaries or post-job analyses, further optimize drilling performance. In deepwater operations, remote control via a single user interface facilitates automatic riser installation, complete closure of the Annular Isolation Device (AID), RCD locking and unlocking, and flow path control. From well design and real-time operations to post-job summaries, all data remains consistent. Management of real-time visualization and engineering assessment/planning aspects is handled through the CENTRO Well Construction Optimization platform.
Current developments include the use of high-pressure flow meters (installed on the riser) to replace simple pump stroke counters for improved flow measurement. With this new technology, the rheological properties and mass flow characteristics of the fluid entering the closed-loop drilling circuit can be compared with the measurements of returning fluid. Compared to traditional manual mud measurement methods with much lower update frequencies, this system offers superior hydraulic modeling and real-time data.
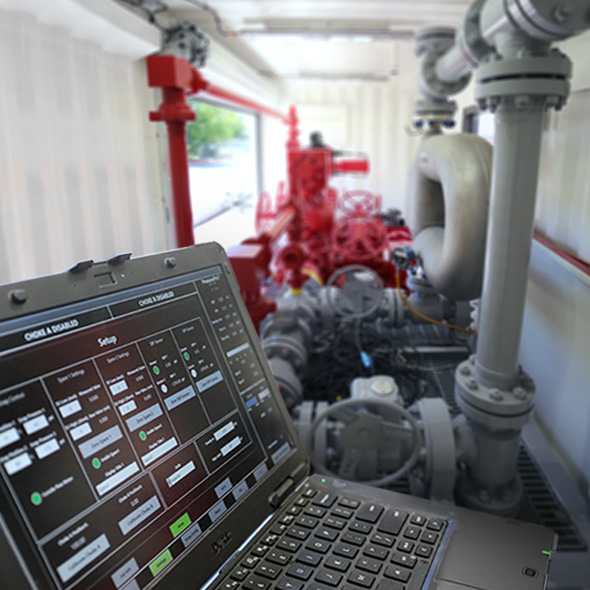
04. Providing Simple, Precise Pressure Control and Data Acquisition
The PressurePro and Victus technologies are solutions developed for entry-level and advanced pressure control applications, respectively. Weatherford recognized that there are applications suited for solutions falling between these two levels. The company's latest Modus MPD solution fills this gap. Designed for various applications such as high-temperature or low-temperature environments, onshore, and shallow water, the system's goal is straightforward: to focus on the performance advantages of pressure control technology, enabling operating companies to drill more efficiently and reduce pressure-related issues.
The Modus solution features a modular design for flexible and efficient installation. Three devices are housed within a single shipping container, requiring only one lift during on-site unloading. If needed, individual modules can be removed from the shipping container for specific placement around the wellsite.
The choke manifold is one independent module, but if there's a need to install it within existing infrastructure, the system can be configured to meet the specific requirements of each drilling platform. Equipped with two digital control choke valves, the system allows flexible use of either valve for isolation or combined use for higher flow rates. Precise control of these choke valves improves wellbore pressure and Equivalent Circulating Density (ECD) control, enabling more efficient drilling with lower mud densities. The manifold also integrates an overpressure protection system and piping.
The flow measurement device is another module. Using Coriolis flow meters, it measures returning flow rates and fluid properties, recognized as an industry-standard for accuracy. With continuous mass balance data, operators can immediately identify downhole pressure changes appearing in the form of flow anomalies. Real-time visibility of well conditions facilitates quick responses and adjustments, addressing pressure issues before they impact operations.
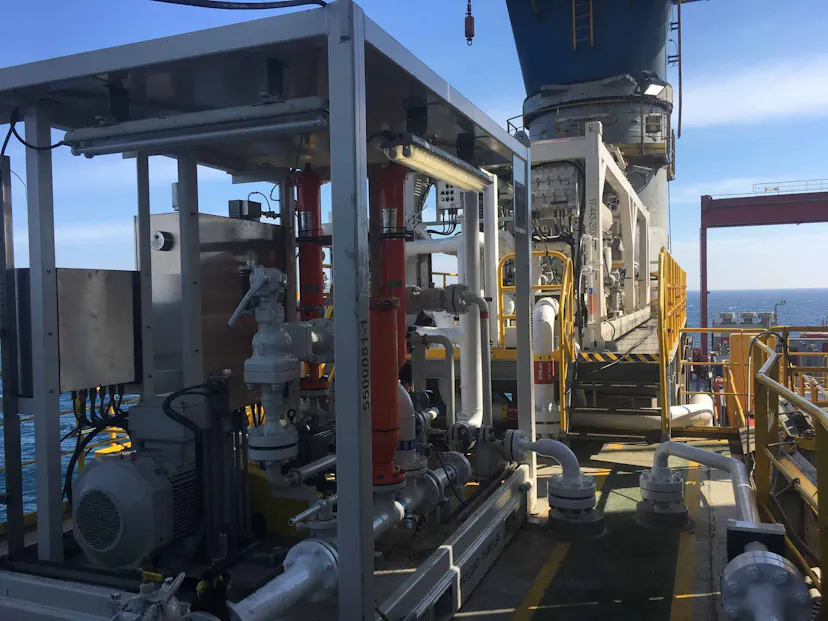
The digital control system is installed within the third module and is responsible for managing the data and functions of the measurement and control devices. This digital platform operates through the HMI of a laptop, allowing operators to view measurement conditions with historical trends and control pressure through digital software. Charts displayed on the screen provide real-time trends of downhole conditions, enabling better decision-making and quicker responses based on the data. When operating in constant bottomhole pressure mode, the system can rapidly apply pressure during connection periods. With a simple button press, the system automatically adjusts the choke valves to apply the required pressure to the wellbore, maintaining constant downhole pressure without flow. Relevant data is collected, stored for post-job analysis, and transmitted through the Well Information Transmission System (WITS) interface for viewing on the CENTRO platform.
By automatically controlling pressure, the Modus solution can promptly respond to downhole pressure changes, protecting personnel, wellbore, environment, and other assets. As part of the wellbore integrity system, the Modus solution controls Equivalent Circulating Density (ECD), providing a reliable method to enhance operational safety and protect formation integrity, thereby achieving safe drilling within narrow safety windows with multiple variables and unknowns.
Weatherford relies on over 50 years of experience, thousands of operations, and millions of hours of operation time to summarize reliable methods, attracting an Ohio-based operating company to deploy the Modus solution. In the Utica Shale area, the operating company needed to drill an 8.5-inch wellbore to the design depth to meet authorized expenditure cost targets.
Compared to the planned drilling time, the Modus solution shortened drilling time by 60%, completing the entire well section in one trip. The key to this success was the use of MPD technology to maintain ideal mud densities within the designed horizontal section, minimizing wellbore circulating pressure losses. The aim was to avoid potential formation damage from high-density mud in formations with uncertain pressure profiles.
During the basic design and construction design phases, Weatherford's technical experts collaborated with the operating company to define the scope of the horizontal well and set drilling objectives. The team identified requirements and created a service quality delivery plan that not only coordinated project execution and logistics but also reduced overall costs. Weatherford engineers recommended the Modus solution as the best choice for the operating company.
After completing the design, Weatherford field personnel conducted a site survey in Ohio, allowing the local team to prepare the work site and assembly area and identify and eliminate potential hazards. Meanwhile, experts from Texas tested the equipment before shipping. These two teams maintained continuous communication with the operating company to coordinate timely equipment delivery. After the Modus MPD equipment arrived at the drilling site, efficient installation and commissioning were carried out, and the Weatherford team quickly adjusted the MPD operation layout to accommodate changes in the operating company's drilling design.
05. On Site Successful Application
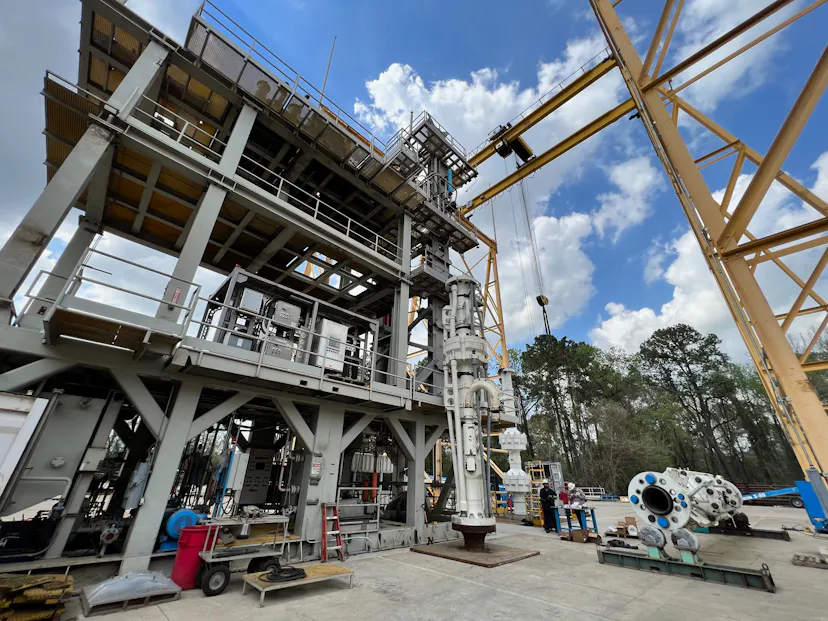
However, shortly after the well was landed, signs of blockage appeared in the wellbore. After discussing with the operating company, Weatherford's MPD team provided the latest operational plan to address the issue. The preferred solution was to increase backpressure while slowly raising the mud density by 0.5ppg (0.06 SG). This allowed the drilling rig to continue drilling without waiting for mud adjustments and without significantly increasing mud density. With this adjustment, the same bottomhole drilling assembly was used to drill to the target depth of the horizontal section in one trip.
Throughout the operation, the Modus solution actively monitored wellbore influx and losses, allowing the operating company to use drilling fluids with lower densities and reduce the use of barite. As a complement to low-density mud in the wellbore, Modus MPD technology actively applied backpressure at the wellhead to easily handle the continuously changing downhole conditions. Traditional methods typically take hours or a day to increase or decrease mud density.
By applying Modus technology, the operating company drilled to the target depth nine days ahead of the design days (15 days). Additionally, by reducing mud density by 1.0 ppg (0.12 SG) and adjusting backpressure to balance downhole and formation pressures, the operating company reduced overall costs. With this Weatherford solution, the horizontal section of 18,000 feet (5486 meters) was drilled in one trip, increasing the Mechanical Rate of Penetration (ROP) by 18% compared to four nearby conventional wells.
06.Outlook on the Future of MPD Technology
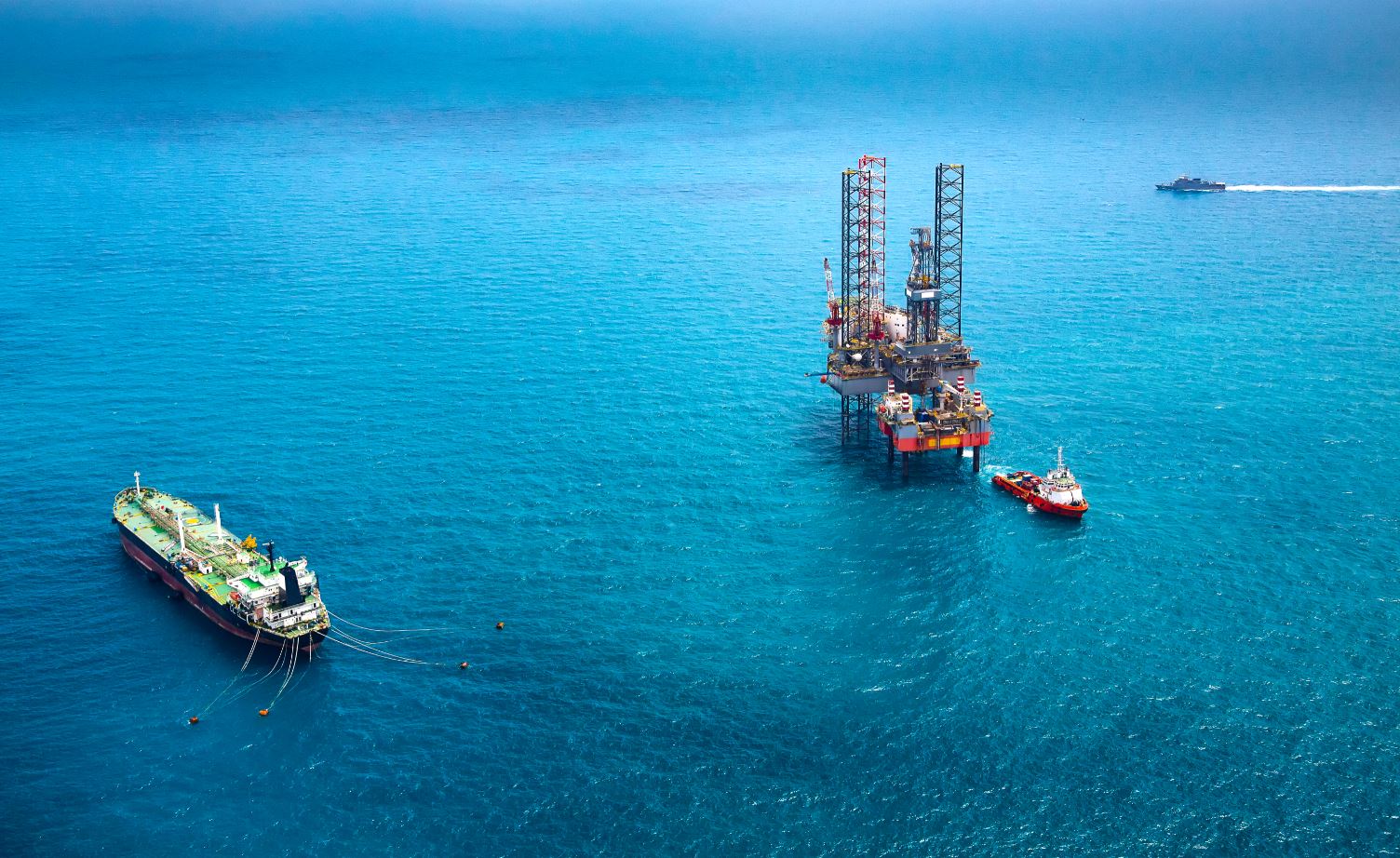
The cases outlined above, where value is created through performance enhancement, are just one example of the broader application of Weatherford's Modus solution. By 2024, a batch of systems will be deployed worldwide to further expand the use of pressure control technology, allowing other operating companies to understand and achieve long-term value with fewer complex situations and higher well construction quality.
For many years, the energy industry has only applied pressure control technology during drilling operations. Weatherford has a different view on pressure control. It's a performance enhancement solution applicable to numerous, if not all, categories of oil wells, including horizontal wells, directional wells, development wells, multi-lateral wells, and more. By redefining the objectives that pressure control in the wellbore can achieve, including cementing, running casing, and other operations, all benefit from a stable wellbore, avoiding wellbore collapse and formation damage while increasing efficiency.
For example, controlling pressure during cementing allows operating companies to more proactively address downhole events such as influx and losses, thereby improving zonal isolation. Pressure-controlled cementing is particularly effective in wells with narrow drilling windows, weak formations, or minimal margins. Applying pressure control tools and technology during completion operations allows for easy pressure control during the installation of completion tools, improving operational efficiency and reducing risks.
Better pressure control within safe operating windows and applicable to all wells and operations. With the continuous emergence of Modus solutions and pressure control systems tailored for different applications, pressure control in more oil wells is now possible. Weatherford's solutions can provide comprehensive pressure control, reducing accidents, improving wellbore quality, increasing wellbore stability, and enhancing production.
Post time: Mar-20-2024